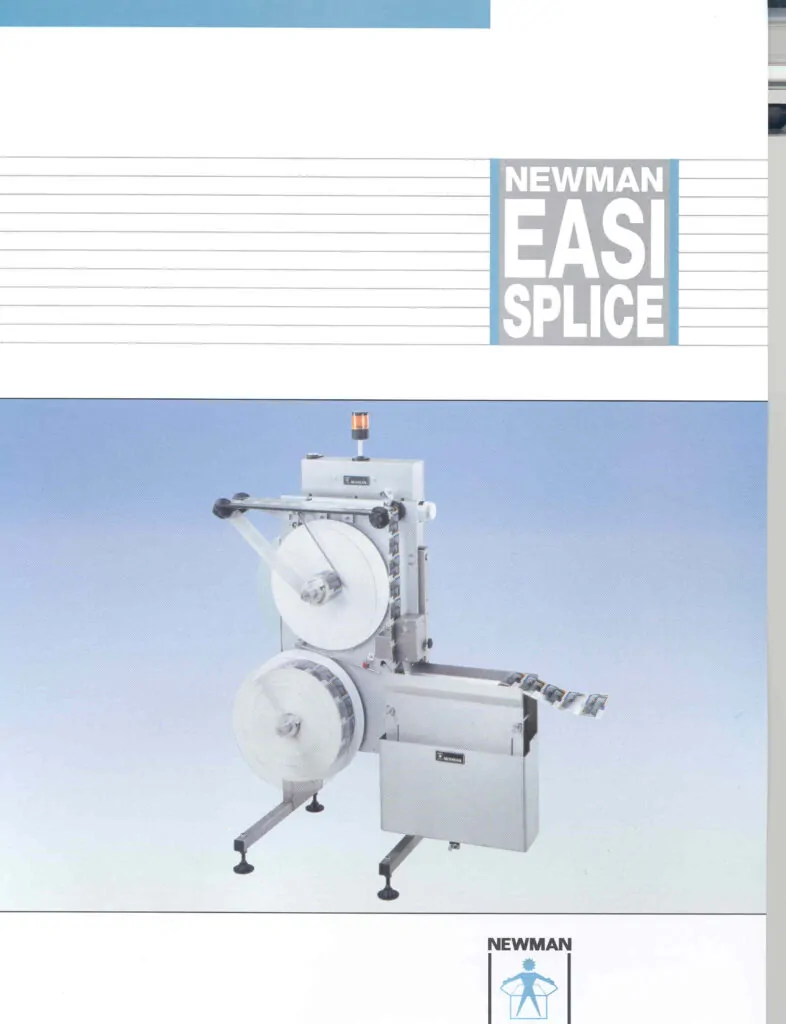
This report explores the Benefits and Cost Savings of the Easisplice 470 System, a free-standing reel splicing unit designed to revolutionize high-throughput production environments. The Easisplice 470 eliminates downtime during label reel changes, offering a seamless, efficient solution for industries such as pharmaceuticals, food processing, and other manufacturing sectors.
Key Benefits and Cost Savings of the Easisplice 470 System
1. Continuous Label Feed for Maximum Efficiency
At the core of the Benefits and Cost Savings of the Easisplice 470 System is its ability to maintain an uninterrupted label supply. The system allows reel changes to occur without stopping production, ensuring maximum uptime in fast-paced manufacturing lines.
2. Increased Production Speed & Throughput
The Easisplice 470 supports high-speed labeling up to 64 meters per minute. This leads to increased output and throughput, a crucial component in understanding the specifications, especially in high-volume operations.
3. Reduced Downtime-Related Costs
One of the key benefits and cost savings of the Easisplice 470 system is the elimination of costly production stoppages. By allowing reel changes on the fly, the system helps reduce labor expenses, labeling errors, and operational inefficiencies.
4. Flexible, Easy-to-Use Design
The Easisplice 470 is designed for seamless integration with most labeling machines. Its free-standing configuration, tool-free adjustments, and left/right-hand options make it a highly adaptable system, further contributing to the overall efficiency through faster setups and changeovers.
5. Waste Reduction & Sustainability Advantages
Minimizing waste is a critical component of the Esaisplice 470. The integrated buffer bin system ensures labels are used efficiently, reducing material waste and supporting sustainability efforts.
6. Operator Efficiency and Workload Reduction
Automatic reel-end detection and operator alerts allow staff to focus on other value-added tasks instead of monitoring the label supply. This enhanced operator efficiency is another key factor contributing to the cost savings offered by the Easisplice 470.
7. Noise Reduction for a Healthier Work Environment
Operating at less than 75 dB, the Easisplice 470 fosters a quieter work environment, lowering the need for additional noise control measures—an often-overlooked aspect of production cost savings.
Cost Savings Breakdown
The following table illustrates how the Benefits and Cost Savings of the Easisplice 470 System compare to traditional reel change processes:
Category | Traditional Reel Change | With Easisplice 470 System | Savings Impact |
---|---|---|---|
Production Downtime | Frequent machine stops for reel changes | Continuous labeling with no stoppages | Increased throughput and uptime |
Labor Costs | Higher operator involvement in reel changes | Minimal manual intervention | Reduced labor hours and expenses |
Label Waste | Label misalignment and wastage during stoppages | Optimized label use with buffer system | Lower material and disposal costs |
Setup & Adjustment | Time-consuming, tool-based adjustments | Quick, tool-free setup and changeover | Faster production line resets |
Error Reduction | Higher risk of human error during reel changes | Automated reel-end detection and buffer feed | Fewer labeling and production errors |
Operator Efficiency | Operators must monitor label reels continuously | Operators only intervene when notified | Increased focus on critical tasks |
Conclusion: Why the Benefits and Cost Savings of the Easisplice 470 System Matter
The Easisplice 470 is a valuable investment for manufacturers aiming to improve operational efficiency while reducing costs. The system features include eliminating downtime, reducing labor involvement, cutting waste, and supporting sustainable practices.
For industries operating in high-speed environments, this system enhances throughput and operational reliability while offering tangible financial benefits.
Key Takeaways
- ✅ Continuous labeling → Reduced production stoppages
- ✅ Lower labor costs → Minimal operator intervention
- ✅ Less waste → Cost-effective and eco-friendly
- ✅ Improved efficiency → Higher output with less supervision
- ✅ Quieter work environment → Healthier and more comfortable for staff